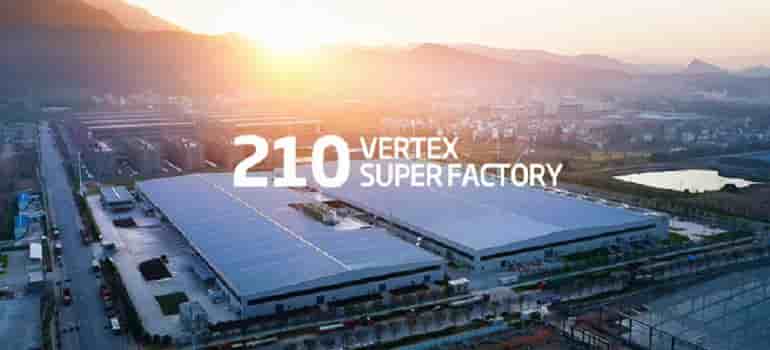
Trina Solar has recently in a press statement said that they have built three Vertex Super Factories in Yiwu, Zhejiang, as well as Suqian and Yancheng in Jiangsu, China.
By the end of 2020, Trina Solar will see its 210mm-module production capacity exceeding 22GW, and will further shoot over 50GW in 2021 across the globe.
Being a Climate Samurai and firm believer of promoting renewables along with reducing carbon footprint, we reached out to the firm with our set of question to know if the factories of the renewable energy firm are really green? We asked –from where new factories are getting power to meet their daily requirement, how these factories are operating , number of workforce and is there any roadmap to minimize carbon footprint ?
Here is what the spokesperson of the company said : –
Trina Solar plays an important role in setting new benchmarks for the global industry by fostering best practices, world-class quality standards and sound policies. Trina Solar is committed to providing clean, sustainable solutions throughout the entire manufacturing life cycle of its products.
- For Yancheng module factory, the factory is operating and maintaining by local power grid, a single workforce has 450 labor forces. They use lower-energy motors to reduce the carbon emissions.
- Suqian cell factory: it selectively use company’s own modules installed on the rooftops to generate power. A single workforce has 40 labor force per line, which are 320 labor forces in total. They have Heat Recovery System, RO concentrated water recycling and electric energy saving.
- Yiwu module factory: new manufacture base is planning to use Trina Solar’s own modules to install on the rooftops. 1600 labor forces (including 2nd phase). They use Heat Recovery System.
The development of the 210mm industry chain has matured, where most customers recognize and accept the related products. Let’s take quick trip through these Trina Solar 210 Super Factories.
The Vertex Super Factory project in Yiwu has progressed rapidly, completing the infrastructure and move in the equipment in just 112 days. On July 29, Trina Solar’s Yiwu production base started production of 4GW modules for the first phase. The groundbreaking ceremony for the second phase of 4GW modules was held on the same day. This is the world’s first factory base producing innovative and ultra-high-power products of 210mm silicon wafers, cells and modules. The factory has marked an important milestone in the history of Trina Solar while taking the industry to a new height.
Vertex Suqian 210mm- module plant has a capacity of 12GW, where the first and second phases are now operating. The third phase, meanwhile, is progressing rapidly. It is expected to complete the groundwork by the end of 2020 and start production in the first quarter of 2021. More Trina Solar Vertex Super Factories in foreign countries are also under preparation.
The Vertex Super Factories are based on cutting-edge technologies and manufacturing techniques that are the most advanced in China’s photovoltaic industry.
In terms of module technology, Trina Solar’s Vertex series modules incorporate several state-of-the-art technologies such as non-destructive cutting, high-density interconnection, and MBB, which are ahead of similar products in terms of power, efficiency and reliability.
Low-voltage, high-string-power design
Vertex 600W+, 550W series modules adopt the innovative design with low voltage and high string power. This design can effectively reduce the number of strings, and the corresponding mechanical connections such as racking structure, DC cables, junction boxes and other electrical connections can be effectively saved, and thus the system cost, thereby adding more value to customers. At the same time, the auto bussing machine equipment has successfully integrated special high-precision placement and automated functionality.
Multi-busbar technology with precisions in millimeters
Trina Solar is the first company in China to develop and realize the industrialization of Multi-busbar technology (MBB). MBB modules use precise positioning and welding solutions to nail down to millimeter-level precision. Round ribbons are applied to improve the secondary optical utilization of the ribbon area. The power, therefore, can be increased by more than 5W compared with 5BB modules, so that the conversion efficiency of Vertex modules can be boosted as much as 0.3%.
The remarkable performance of Trina Solar’s 210 mm modules – high efficiency, high power, high reliability, and significant reduction of BOS and LCOE costs – is made possible by a combination of innovative technologies, reflecting Trina Solar’s 23 years of technological and innovative advancement.
High Level of Automation and Highly Efficient Productivity
In the Super Factory, super intelligence is everywhere. Trina Solar produces Vertex modules with complete automated equipment. The brand-new welding machine can weld at a speed of about 4,000 pieces per hour – currently the fastest in the industry. The laminator is also extremely advanced in terms of power saving and its production speed. The Vertex Super Factory can directly detect product defects through automatic visual inspection equipment using artificial intelligence technology, effectively improving inspection efficiency and product yield.
Compared with previous workshops, Trina Solar’s fully automated workshop can reduce the staff size by about 25% per GW. This is a significant cut in labor, thus the related costs, compared to the current 166mm or 158mm-module factories.
Highly intelligent and advanced, the Vertex Super Factory’s production efficiency has continued to improve, and the detection efficiency and product yield rate are leading in the industry while ensuring high-quality output and maximum utilization of resources. Moreover, with the ultra-high-power characteristics of the 210 modules, the production line’s efficiency is incredibly improved.
Sharing Data with Customers for Smart Manufacture in the 600W+ era
“We already have a complete set of smart factory solutions and smart manufacturing data centers,” said Yang Xiaojun, General Manager of Trina Solar’s Yiwu Super Factory. “Data can help in different areas, such as monitoring the production status of all production facilities, order tracking, and customer order completion. It can be shared with the company’s internal and remote customers in real-time. For customers, they can view the production process and key parameters of the product anytime, anywhere.”
Trina Solar always focus on customer value. Via technological advancement, we bring customers the most cost-effective products with higher power generation efficiency and the best product experience. Trina Solar’s Super Factory have vastly improved the efficiency and speed of innovation in the photovoltaic industry, accelerated the industrialization of 600W+ ultra-high-power module products, and pushed China’s photovoltaic industry forward to lead the world again.
As one of the initiators of the 600W+ Photovoltaic Open Innovation Ecological Alliance, Trina Solar stands at the forefront of the new photovoltaic era! With super factory, super innovation, and super revolution, Trina Solar always takes customer value seriously, while driving the sustainable growth of the photovoltaic industry and leading the industry into a green future.
Climate Samurai has small but strong editorial team that brings you uninfluenced and curated news that you can trust. To support truly independent journalism, please consider taking a subscription which is free like our thought.